Meeting enormous energy challenges comes with the territory for Recycled Energy Development (RED) Rochester, the utility that owns and operates the trigeneration heating, cooling, and power utility infrastructure for Eastman Business Park. Located in Rochester, New York, three miles from Lake Ontario, Eastman Business Park is a massive innovation hub that evolved from Eastman Kodak’s 1,200-acre photographic film manufacturing campus. Today, the campus houses more than 100 enterprises in 16 million square feet, an area equivalent to 277 football fields. Tenants consume massive amounts of electricity and multiple utility services, including chilled water for comfort and process cooling.
For process and comfort cooling at Eastman Business Park’s south campus, RED Rochester employed several steam turbine-driven centrifugal chillers — two for primary duty and one for backup — to provide 43°F chilled water. But, RED Rochester is always interested in reducing energy costs and its carbon footprint. When it came time to replace the backup steam-turbine chiller, RED Rochester was intrigued by a proposal about using an electric chiller made by Smardt. Estimates showed the efficiency of a Smardt centrifugal chiller with Danfoss Turbocor® magnetic-bearing compressors could cut $650,000 annually off the gas bill and reduce CO2 emissions by more than 23,300 metric tons, a huge economic and environmental benefit.
Why a Single Large Chiller Makes Sense
Owned by Ironclad Energy Partners, RED Rochester owns and operates its 120-megawatt (MW) utility service as a “microgrid”— a system of interconnected loads and distributed resources grouped “inside the fence” of Eastman Business Park. As a result — although nested within the Rochester Gas and Electric (RG&E) service territory — RED Rochester makes real-time utility-operating decisions independently. It can import or export power and increase or decrease steam and electric production to run as reliably and cost-competitively as possible. RG&E provides RED Rochester with natural gas to power its tri-generation power plant. RG&E also offers rebates when customers can apply technology to reduce consumption. RED Rochester eagerly investigated the new Smardt chiller that promised to more effectively utilize its gas-fired infrastructure for powering electric refrigerant compressors rather than steam-turbine-driven compressors.
“It’s been nearly 20 years since a new electric chiller was purchased and installed at Eastman Business Park,” said Craig Avalone, energy manager for RED Rochester. “Historically, the standard selection for a new electric chiller would have been an industrial-duty centrifugal chiller with a single oil-lubricated compressor. However, with our focus on energy efficiency and reliability, we investigated the advantages of oil-free electric chillers using magnetic-bearing centrifugal compressors.”
Rob VanSkiver, Rochester-area sales engineer for H&V Equipment Sales, was impressed by the research Avalone’s engineering team conducted.
“They investigated magnetic-bearing centrifugal chillers in general, but also the specific advantages of selecting a multiple-compressor Smardt chiller,” he said. “RED Rochester was also receptive to using a single chiller with 2,000 ton of refrigeration (TR) capacity over the initial design of multiple chillers. The final selection was a Smardt V-Class magnetic-bearing chiller using R-134a refrigerant and employing five Danfoss Turbocor VTT magnetic-bearing compressors with Danfoss variable frequency drives.”
This solution contrasts with the original scope of work that called for two 1,000-TR magnetic-bearing centrifugal chillers. After careful consideration, Avalone’s team realized going with a single 2,000-TR chiller offered many advantages. A single large chiller would dramatically reduce costs of rigging and assembling the chiller into the second-floor equipment room and the expenses of additional pumps, piping, insulation, electrical connections, instrumentation, and controls. Going with an oil-free design would also eliminate the hassles of installing and maintaining an oil lubrication system.
“The only machine at the time with 2,000 TR capacity in an oil-free design was the Smardt V-class water-cooled chiller,” said VanSkiver. “To deliver that capacity, it uses five Danfoss Turbocor VTT compressors, each with a nominal 400 TR capacity [2,000 TR total].”
The multiple compressors are arrayed in a reliable modular configuration. No single compressor failure can bring the chiller down. Modularity also enhances flexibility because the compressors can be stagingd to run like multiple machines. As the load decreases, compressors cycle off to turn down capacity to 10% of full-load rating. As the load increases, additional compressors turn on. When all Danfoss Turbocor VTT compressors are running at full load in conjunction with the Smardt economizer and colder than design condenser water temperatures, the chiller has been able to provide up to 2,300 TR capacity — 300 TR above the nominal rating. The wide capacity range makes it possible to postpone turning on less efficient steam-turbine-driven chillers, since the additional load can be handled in cool weather by the electric chiller. The Smardt V-class chiller also incorporates Danfoss ball valves, sight glasses, solenoid valves, KVS electronic-suction modulating valves, and ICM motor-operated valves to enhance performance.
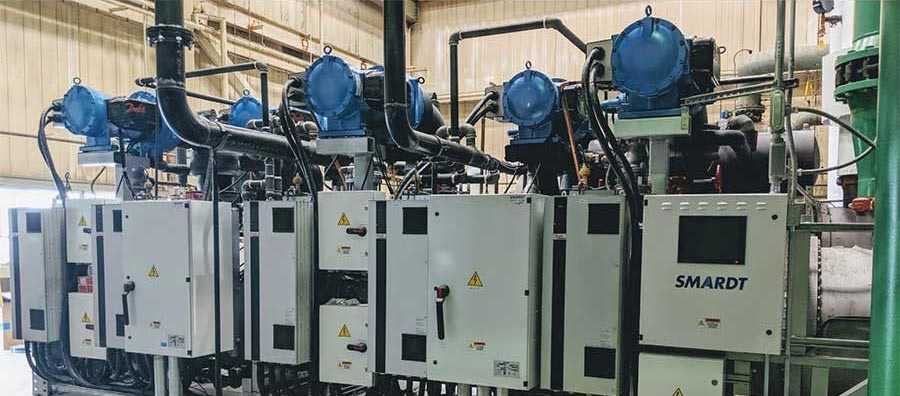
Variable-Speed Operation for Variable Weather
The weather varies significantly in Rochester, New York. Proximity to Lake Ontario brings a changing mix of humidity, rain, snow, freezes, and thaws. In colder weather, chillers operate in part-load conditions compared to the full-load conditions of summer.
The old steam turbine chillers were not designed for large load variations and perform poorly in part-load conditions; often, false loading through hot gas bypass was required to adequately reduce capacity. That’s because the old chillers were oversized and used various efficiency-robbing techniques needed to ensure adequate refrigerant and oil flow. In contrast, the Danfoss Turbocor VTT compressor uses magnetic bearings that rotate in a magnetic field. There are no mechanical bearings requiring lubrication. Conventional, single oil-lubricated compressor chillers have limited method of capacity control at low refrigerant flow levels (the “surge” region) and at high flow levels (the “choke” region). Chillers with multiple Danfoss Turbocor VTT compressors with Danfoss variable-speed drives can reduce capacity further by reducing the number of compressors operating to enable outstanding part-load efficiencies while still operating reliably.
Innovative Danfoss IntraFlow™ technology enhances the speed and capacity control of the Danfoss Turbocor VTT compressor. IntraFlow extends the operating range without the need for inlet guide vanes, variable geometry diffusers, and hot gas bypass required on conventional chillers to turn down capacity and maintain stability.
“Eastman Business Park’s load is quite dynamic,” said VanSkiver. “Being able to operate this unit efficiently over a wide load range gives RED Rochester the flexibility of staging compressors to cycle on and off as needed and effectively handle full and part loads. The Smardt chiller ramps up to handle the primary load until a steam-turbine chiller is brought online to carry that load. Then, it ramps down to carry part loads far more efficiently than one of the steam-turbine chillers could. Finally, Danfoss variable-speed drives were applied on the new chilled water and condenser water pumps to enhance overall system performance.”
Thanks to Danfoss Turbocor compressors, the Smardt chiller can take advantage of cold weather conditions to operate at extremely low 45°F condenser water temperatures. In these conditions, it can achieve efficiencies as low as 0.15 kW/TR and a coefficient of performance (COP) up to 25.
Economic and Environmental Benefits
“Our decision to go with one large magnetic-bearing chiller was justified by the energy savings, reduced capital costs, and rebates,” said Avalone. “It gave us a return on investment under two years. The Smardt chiller gives us more bang for our buck because of its outstanding capacity, turndown, and full- and part-load performance.”
Respecting the environment, RED Rochester appreciates the solution’s ability to boost profitability while reducing greenhouse gas emissions. Since the chiller became fully operational in Spring 2019, Avalone feels justified in expecting annual natural gas consumption to drop by 200 million cubic feet.
That translates into cutting CO2 emissions by 23,300 metric ton —the equivalent to taking 2,000 cars off the road.
Originally Posted in esmagazine.com
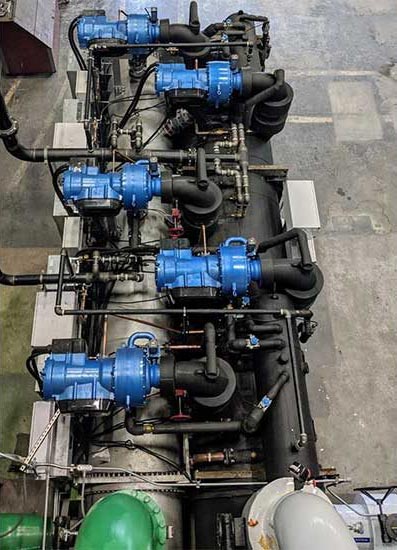